We recently sat down with Ben, our Tech Director at LiberEat, to discuss the interesting work we do to help reduce risks for businesses and keep consumers safe from allergen data errors.
We went into detail about how our technology works and how it differs from other allergen detection techniques in the food safety sphere.
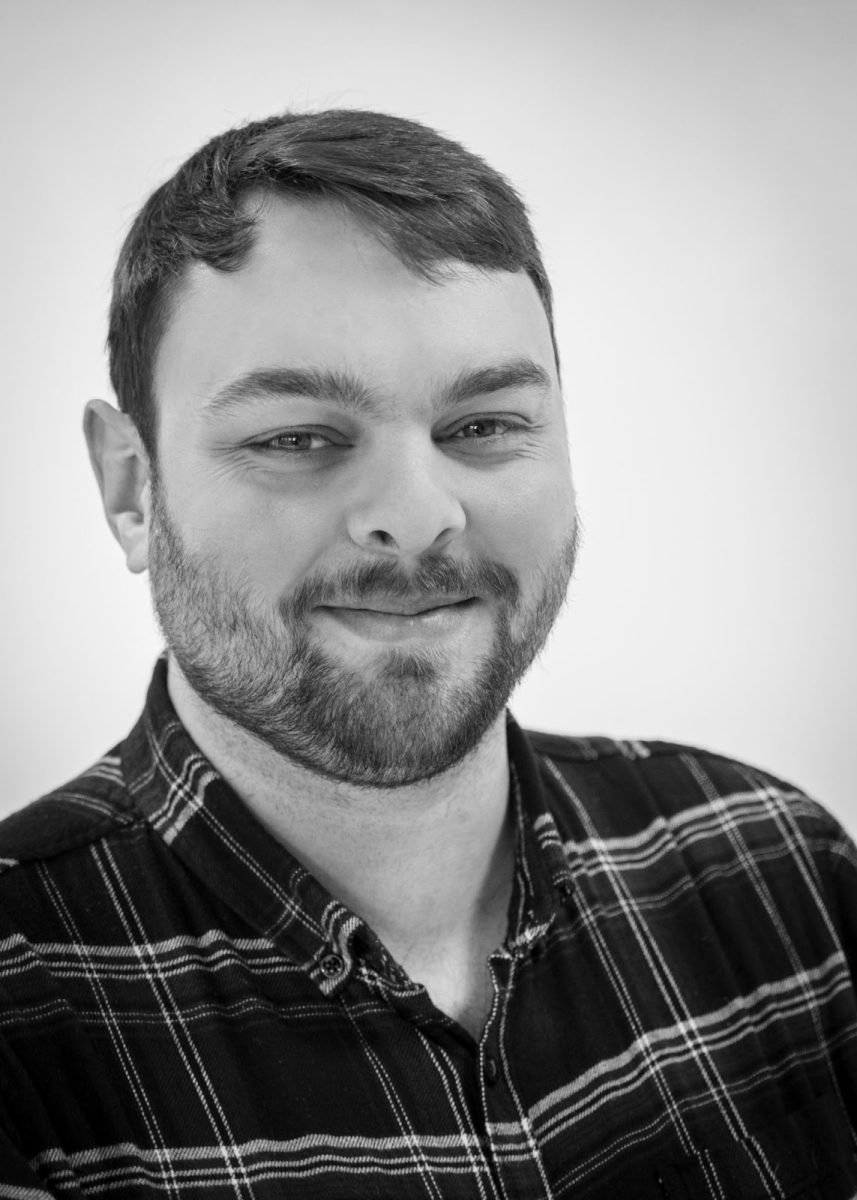
How long have you worked for LiberEat?
I have worked here since 2018. The business has changed a lot since then – We were originally focused on our consumer app, and instead, we are now fully focused on our allergen and error detection software for food businesses.
What is the role of a Tech Director?
It’s essentially someone who is responsible for everything technical. It varies depending on the size and type of company. For us (LiberEat), being a FoodTech company, it means looking at our full product development.
For me, it is about much more than being a product development and being a product owner. That covers everything from the ideas and feature requests that can develop internally or from customer feedback.
Then we have research and development, planning future roadmaps, and generally designing the whole product from start to finish. But at the end of the day, I still get to write a lot of code which is a highlight – so it’s not all just management of projects and tasks – I still get to do some hands-on work.
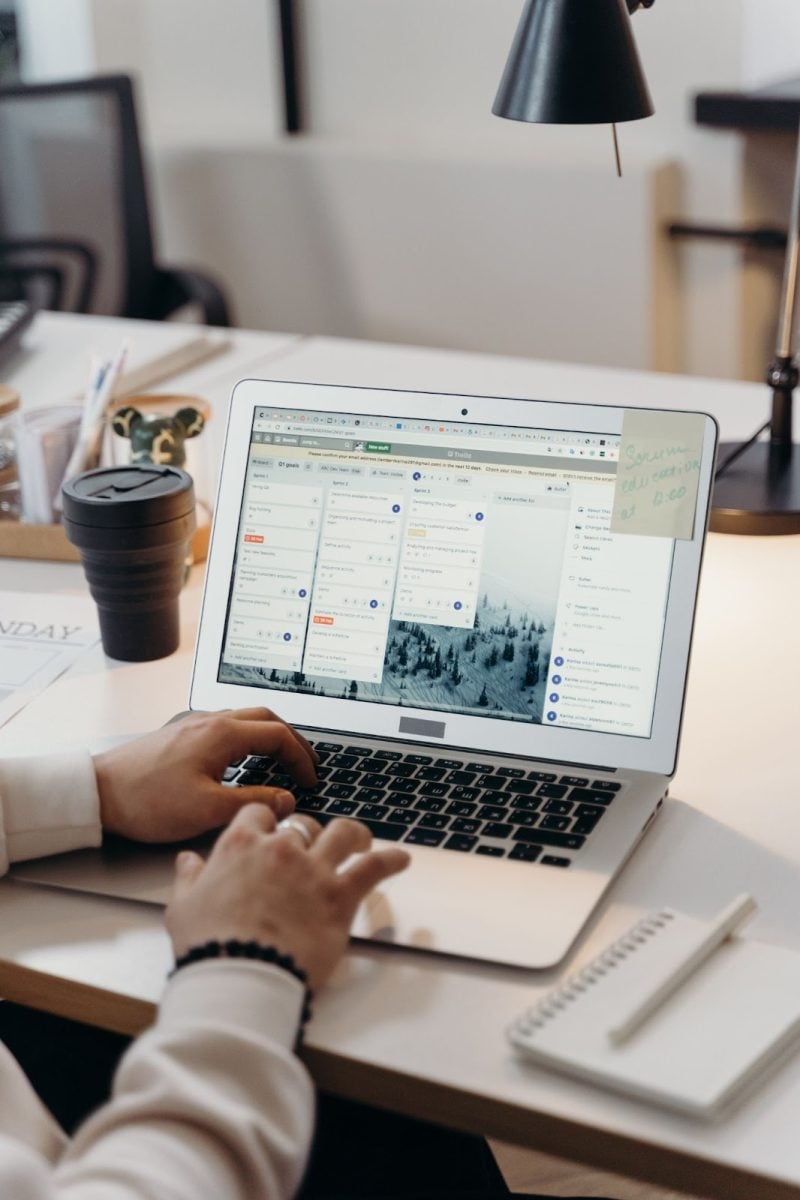
Where are you from, and where do you live now?
I was made and manufactured in the UK.
What does an average day of a Tech Director at LiberEat look like?
Every day is different! A typical workday can look like this:
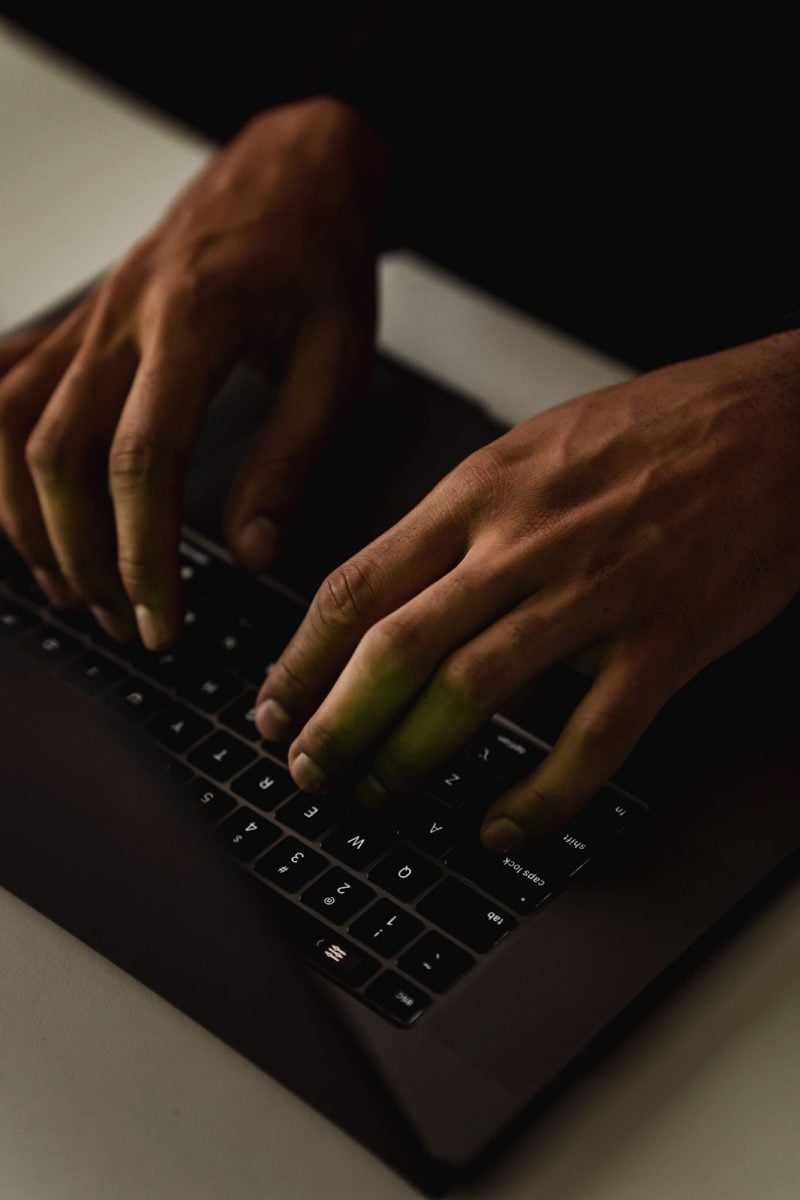
9 am: We have a team meeting to catch up, share news and stay updated on progress and weekly activities.
All departments stay connected with these meetings even if we work on entirely different things. This allows for potential collaboration between departments because if people know what each business area is doing, nobody is missing out on opportunities to support.
10 am: I will call customers and their technical teams on this particular day. Having proper tech-to-tech conversations about integrating LiberEat technology with their systems, which is relatively quick and straightforward.
11 am: The AI development team has a more detailed catch-up of the current sprint.
Lunchtime: I plug myself into the wall to recharge for half an hour, make a sandwich and consume it… everything else at lunchtime is top secret.
1 pm: I like to check in on the customer usage of the platform and make sure everything looks good – a courtesy check if you will.
The rest of the day – Is usually made up of development work, which can include coding and working on our core detection technology.
What's a fun fact about you that people might not know?
I started making websites before we had the internet at home. We had Microsoft FrontPage, and I could make static HTML files on the family computer. I made a bulletin board-style home page for the family. It was full of marquees that were common on websites in the 90s, like scrolling and blinking text.
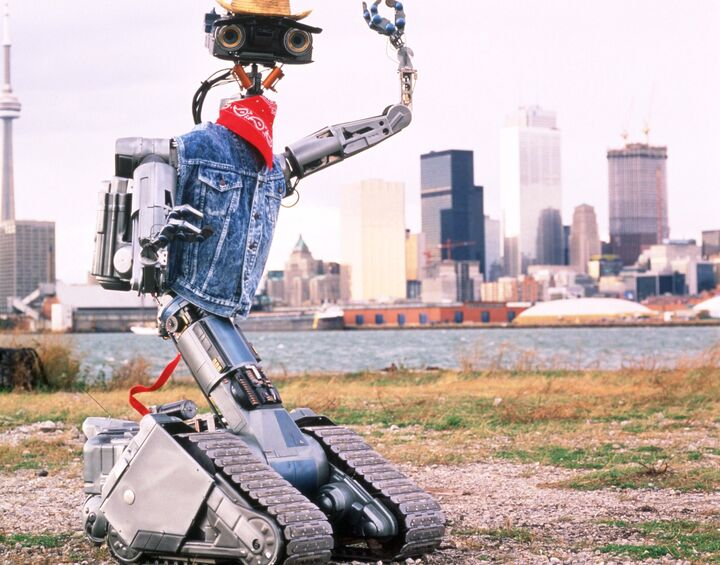
How would you describe yourself in three words?
Not
A
Robot
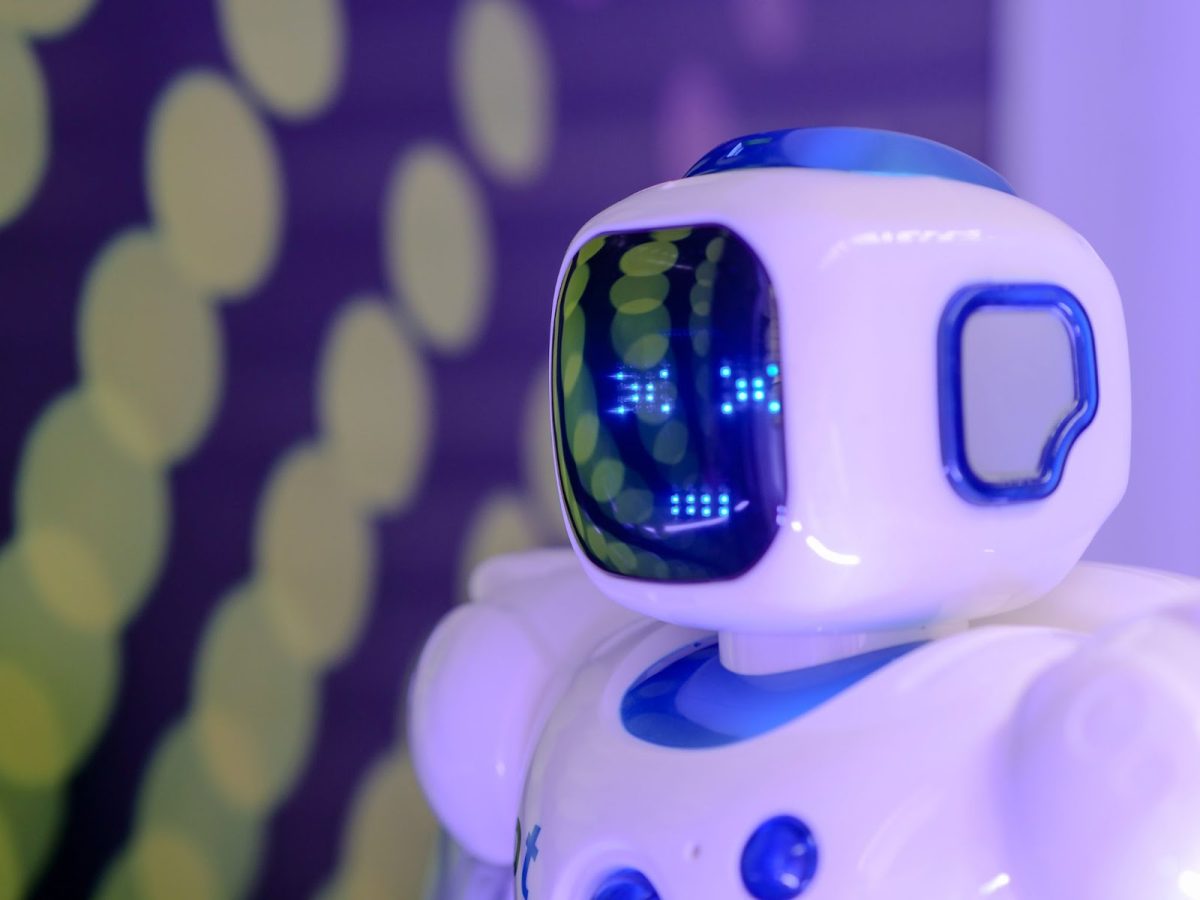
What's one of the best things about working at LiberEat?
One of the best things about working for LiberEat is working for a good cause and mission.
It’s also really exciting being at the early stages of a product and already receiving lots of excellent customer feedback.
This confirms to us that what we are making is unique and groundbreaking. Our product’s customers, mostly food safety professionals, love it, and just knowing this confirms that this is work for positive change.
What role does technology play in allergen detection in the food industry currently?
You might be surprised to learn that technology plays less of a part in the food industry than expected in other industries. There is a lot of emphasis on the (human) manual nature of checking and inputting data. Current technologies include suppliers and stock management systems that link up to the till system.
I see huge advancements in the future in terms of the level of sophistication within the food tech sphere. Many places in the food industry rely on manual processes and aren’t using tech to its full potential – that’s where LiberEat comes in!
How does LiberEat use data to identify allergens and promote food safety?
Our technology intensely monitors food data and detects and alerts customers to any potential issues – mostly allergens and errors in allergen declarations. This allows food safety professionals to check and solve the problem, stopping that error from reaching consumers.
Every customer we have spoken to has the same worries that keep them up at night. Worries that we are uniquely capable of putting to rest.
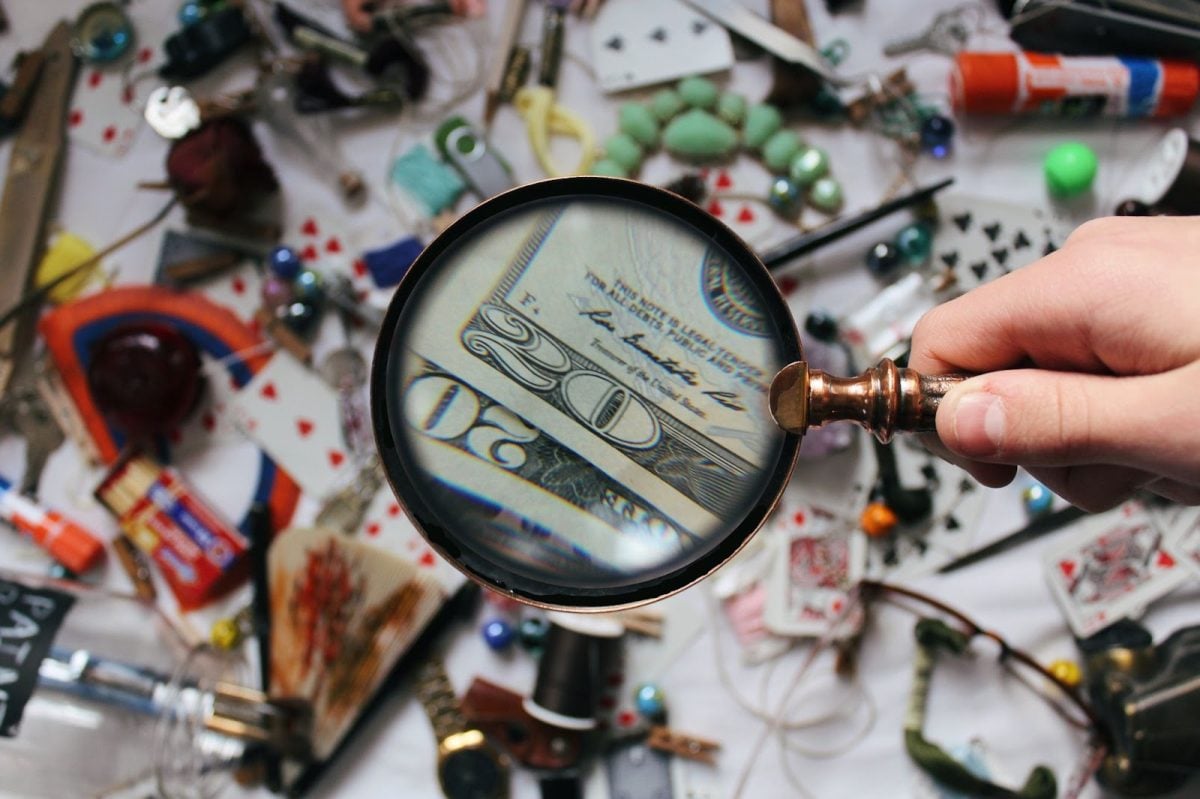
Why do you think LiberEat technology is important?
No other company is solving this problem in the way we are.
The reason LiberEat started was to make food safer for everyone.
As we have been developing the technology over the years, nothing has become more evident to us than just how widespread food allergen errors are. For such a serious issue, it is alarming how often errors can be missed by existing industry methods.
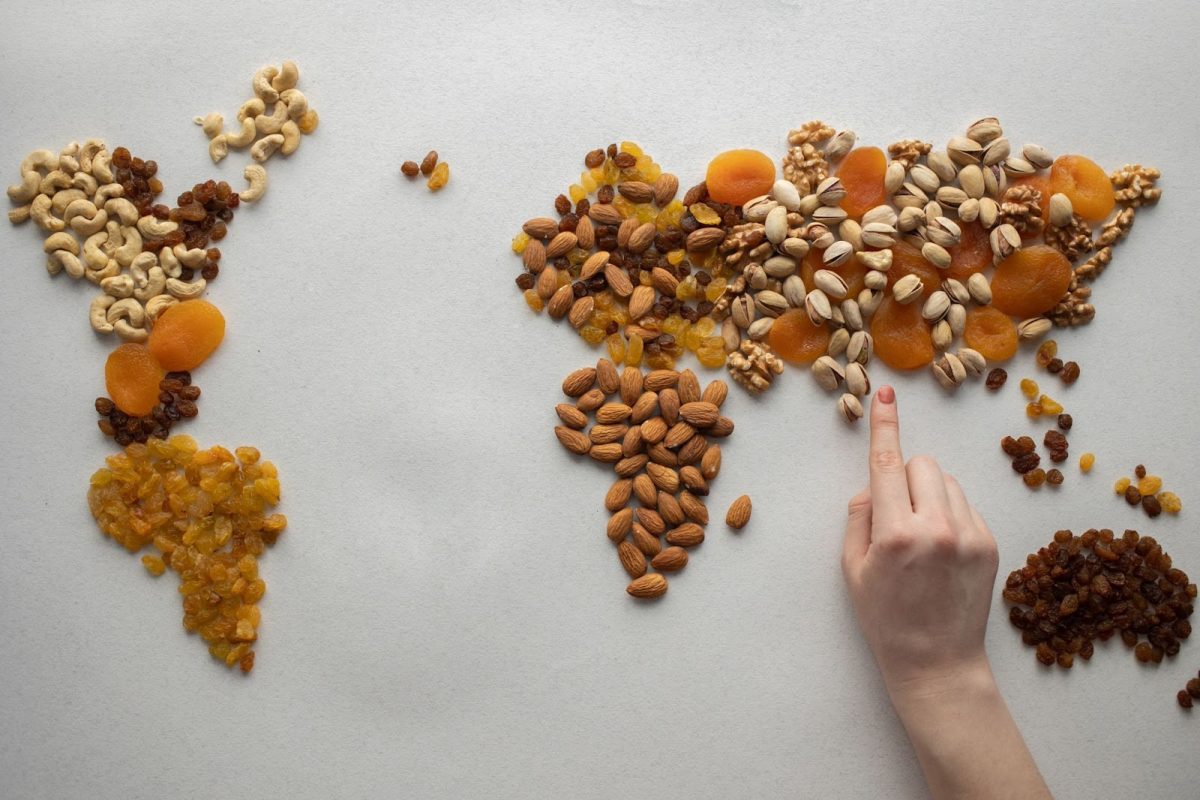
What are some of the most exciting things happening in food tech right now?
There has been a lot of buzz around emerging food technologies recently. What I want food tech to mean is a cool, innovative, exciting technology, and I’m looking forward to seeing what’s next as more companies start developing in this space.
What's the most interesting thing you have learnt since working at LiberEat?
Much of what I have learnt is technical based, finding new solutions to problems and new ways to solve them. We are constantly troubleshooting and utilising techniques used in entirely different fields and industries that can be applied to food safety.
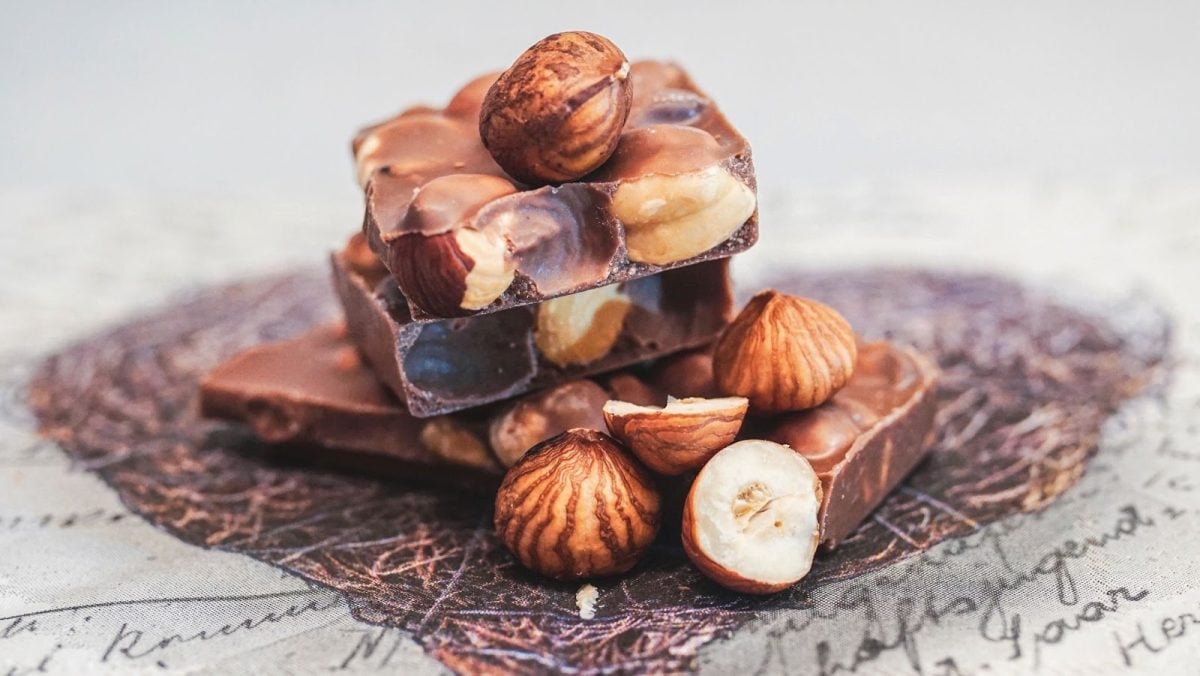
What inspired the development of this technology, and what challenges did you face during its creation?
The main inspiration for developing this unique technology was when we discovered that food data errors, especially with allergens, are so widespread.
With our previous consumer-facing app, we saw how many products and menu items had incorrectly labelled allergens. Then we realised with our technology we could go further up the supply chain and prevent these errors reaching consumers in the first place. This pivot allows us to tackle the original and more widespread issues across the food industry.
Previously, we were at the river’s end with the consumer app, trying to catch all the plastic floating down – with major challenges.
However, now, as a business, we have travelled further upstream and found the person who keeps dumping plastic waste into the river. We are basically gathering the waste before it gets into the river. By catching the problems earlier, we allow all the people downstream to have fresh, safe water.
Can you talk about any success stories or notable instances where your technology has helped prevent food allergy incidents or detect errors in food data?
By putting data through our LiberEat platform, we have sadly found live errors that exist on menus and labels – even things as straightforward as not mentioning milk as an ingredient in a brie sandwich.
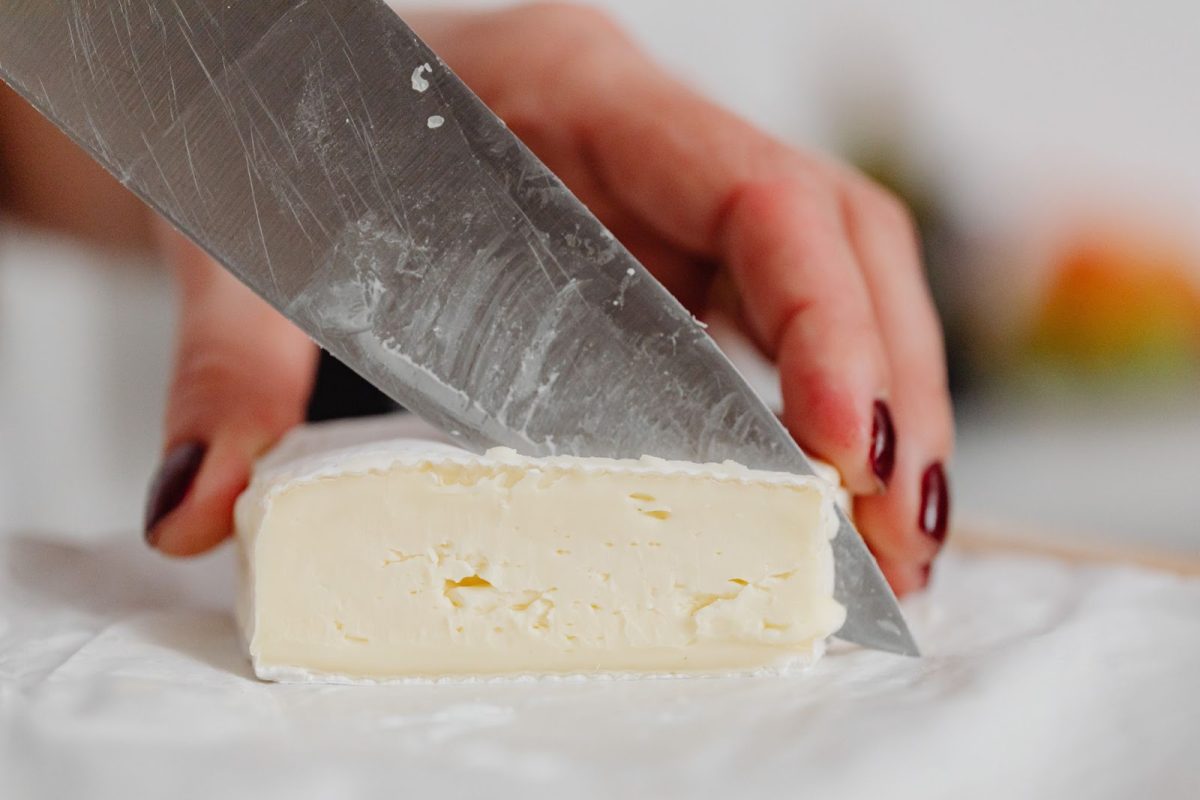
Measuring our success is hard because no one will suffer from an allergic reaction if we do our job right. It is similar to an IT department; no one tends to realise they exist when they do their job well.
What would you say is LiberEat’s approach to addressing the issue of food safety?
The further upstream we can place our technology, we can massively reduce the cascading effect of errors and start protecting people who don’t even use our technology directly. For example, if we work with a supplier, inherently, all of their customers would be protected to some degree as well. The further up to the source we go, the more of a positive impact it has on consumers.
How do you see the future of food safety technology evolving, and what role does LiberEat play in that evolution?
As more companies modernise their systems and processes, food safety will stop being an afterthought and become something that happens as a proactive investment—becoming a standard part of the process, like how no one questions the use of passwords anymore.
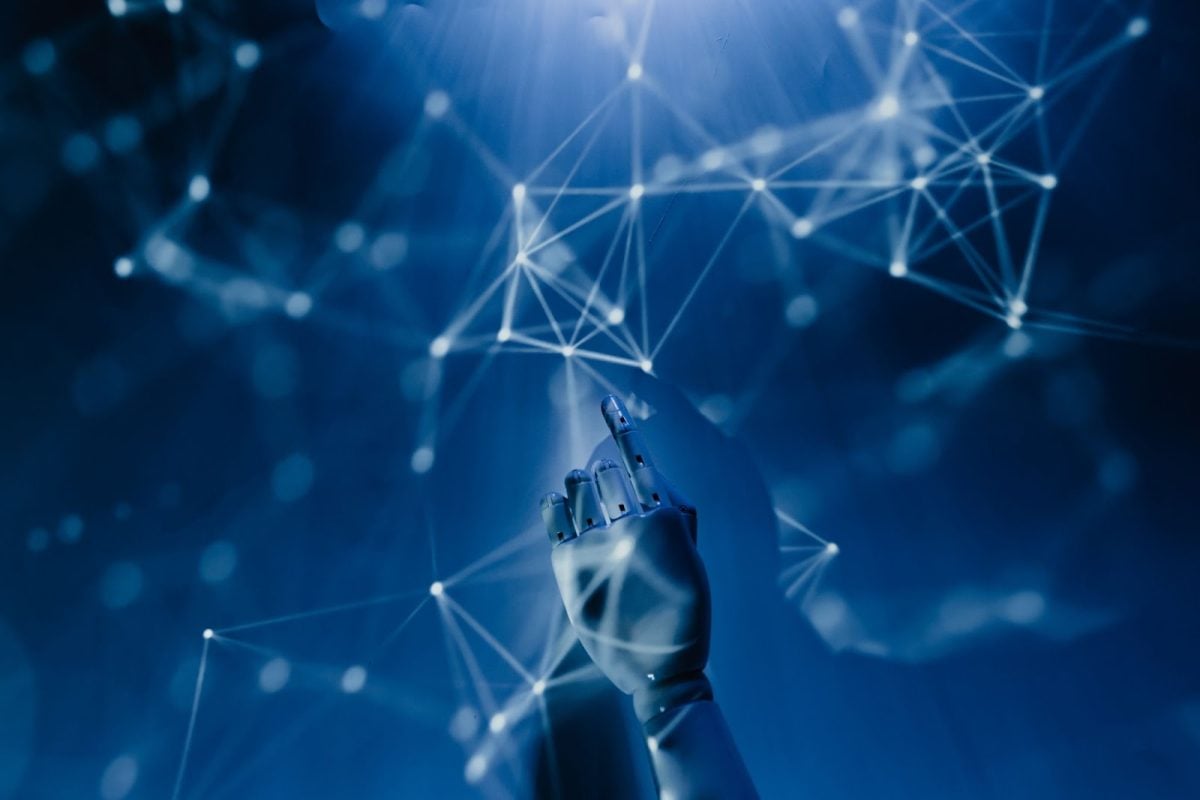
The terms ‘machine learning’ and ‘AI’ are terms that are thrown around a lot nowadays. Here at LiberEat, we have been using it before it was ‘cool’ – we even have our own machine learning engineers accelerating this.
You can learn more about how we use AI at LiberEat from our interview with our machine learning engineer Aradia!
What do people not know about LiberEat?
My username and password!
But seriously, people don’t know about LiberEat- consumers especially. We are like a secret superhero working in the background, helping keep food data safe. You won’t see our sticker in the front of the store (yet), but it doesn’t mean we aren’t keeping a watchful eye.
How would you describe LiberEat in three words?
Important
Adaptive
State-of-the-art (which is hyphenated, so allowed)
What do you like or love about your job?
I like that we are a relatively small but fast growing team meaning that everyone can help everyone. You are not stuck fitting in a box that your job title dictates. There is much more scope for understanding the wider business and product challenges from start to finish.
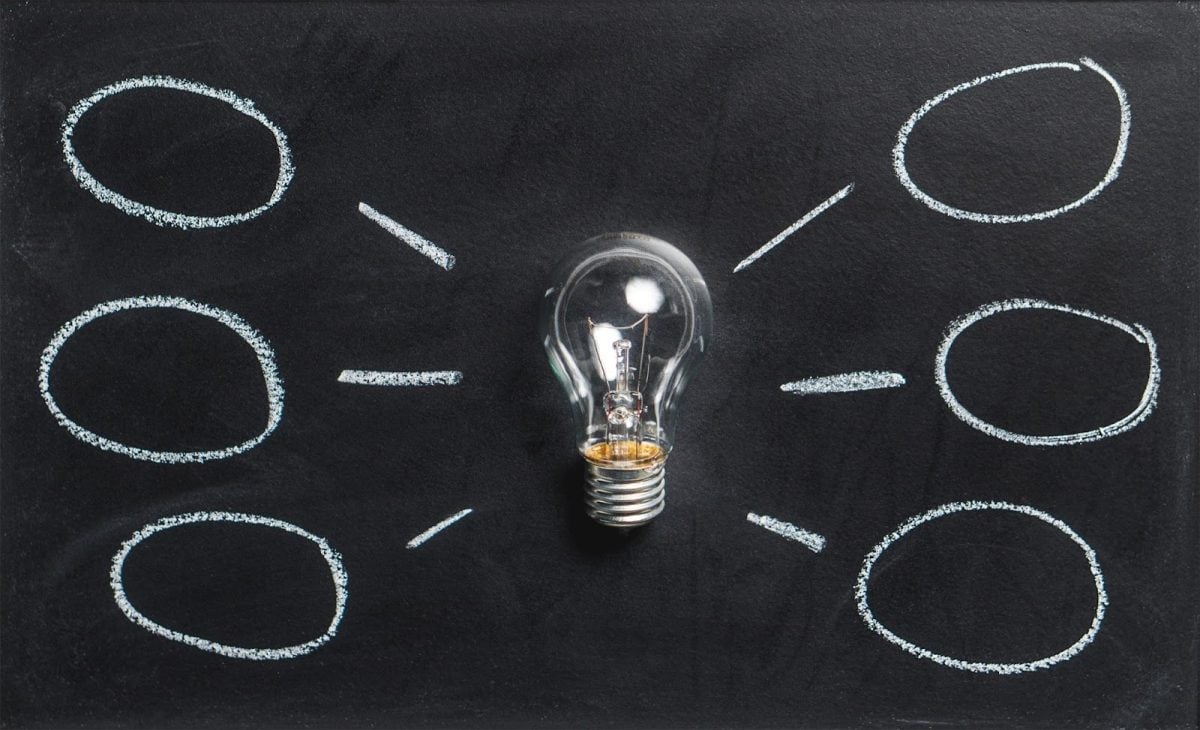
That means I’m doing everything from developing to product design, development operations, hosting, and dealing with our infrastructure. We all have a fair share in the general company. We can have team meetings where everyone can chip in on something, and it can affect our path.
Thanks, Ben!
We’ll be introducing more of our team soon, so stay tuned!
Learn more about our allergen and error detection technology platform for food businesses – we catch the errors that manual processes miss.
Think you know everything about the 14 major food allergens? Find out by taking our allergen quiz and visit our Allergen Information Hub covering everything about these main allergens in the UK.
Visiting from the US? Learn about the nine major food allergens in the US.